|
 |
|
 |
|
Plastic dip-coating
Polythene is a common thermoplastic
powder which is used for dip coating. Air
is blown through the powder which makes
it act like a liquid. Before dipping the
metal is pre heated to 180 degrees and it
is then dipped in the fluidised powder and
returned to the oven where it melts to form
a smooth finish. It is used commercially
for products such as dishwasher racks. It
is often used on school projects for coat
hooks and tool handles.
|
 |
|
|
 |
Powder
coating
Powder coating
is similar to plastic dip coating but is
a more sophisticated process which is mainly
used in industry. The powder is sprayed
onto products which run through an oven.
Powder coating is exceptionally hard-wearing.
Current powder coating technology provides
a finish similar to paint and is available
in all colours and even has a clear option.
|
Anodising
Anodising is a process used
on aluminium to provide a hard-wearing corrosion-resistant
finish. The anodising process involves electrolysis
and uses acids and electric currents. Colour
can be added to the anodising process to
tint the aluminium. Anodising is the most
common finishing process used on aluminium.
|
 |
|
|
 |
Plating
Plating is another
process used on aluminium which uses electrolysis.
There are many types although chromium plating
is by far the most common. The thin plating
layer of metal on the surface provides a
durable finish on metals which are prone
to corrosion.
|
Galvanising
Galvanising involves dipping
metal into a bath of molten zinc. The zinc
provides a good corrosion resistant finish
although it does not look that appealing.
|
 |
|
|
 |
Self-finishing
Many products
are self finished, for example injected
moulded products. The mould is highly polished
which means that the same highly polished
surface is transferred onto each product.
|
Enamelling
Some metals can be enamelled
especially copper. Enamel starts out as
a powdered glass mixture this is applied
over the outside of the metal. The metal
is then heated to 1000°C and the powdered
glass mixture melts. The metal is then cooled
and the powdered glass mixture forms a hard
decorative coating. Enamelling is good for
cookers, baths, pans, etc.
|
 |
|
 |
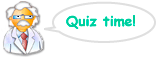 |
|
Mr DT says 'Read the text above and then answer
these questions below'. Write your answers
on a sheet of paper, don't forget to write
your name on the sheet!:-
1). What products is plastic dip coating used
on?
2.) What is the difference between plastic
dip coating and powder coating?
3.) Why is the anodising process used on aluminium?
4.) What is the most common type of plating?
5.) Why is galvanising not necessarily the
best finish for metal?
6.) Name a type of self finished product?
7.) What is the best type of metal to enamel?
8.) Briefly describe the enamelling process?
|
|
|
 |
|
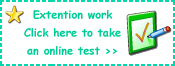 |
 |
|
 |
|
|
|